实验八 精馏实验
一、实验目的
1、了解精馏塔的结构和精馏装置的基本流程及操作方法
2、理解回流比等对精馏塔性能的影响,并实际进行精馏塔的开工操作.
3、学会识别精馏塔内出现的几种操作状态,并分析这些操作状态对塔性能的影响。
4、测定全回流或部分回流操作下的总板效率。
二、基本原理
蒸馏原理是利用混合物中组分间挥发度的不同来分离组分,经多次平衡分离的蒸馏过程称为精馏。由于精馏单元操作流程简单、设备制作容易、操作稳定、易于控制,其设计理论较为完善与成熟,从而在化工企业中,尤其在石油化工、有机化工、煤化工、精细化工、生物化工等企业中被广泛采用。常见的精馏单元过程由精馏塔、冷凝器、再沸器、加料系统、回流系统、产品贮槽、料液贮槽及测量仪表等组成。精馏塔本身又分为板式精馏塔和填料精馏塔。本次实验所用装置为不锈钢制作的板式精馏塔,可进行连续或间歇精馏操作,回流比可任意调节,也可以进行全回流操作。
在板式蒸馏塔中,混合液的蒸汽逐板上升,回流液逐板下降,气液两相在塔板上接触,实现传质、传热过程而达到分离的目的。如果在每层塔板上,上升的蒸汽与下降的液体处于平衡状态,则该塔板称之为理论塔板。然而在实际操作过程中,由于接触时间有限,气液两相不可能达到平衡,即实际塔板的分离效果达不到一块理论塔板的作用。因此,完成一定的分离任务,精馏塔所需的实际塔板数总是比理论塔板数多。
对于双组分混合液的蒸馏,若已知汽液平衡数据,测得塔顶馏出液组成Xd、釜残液组成Xw、液料组成Xf及回流比R和进料状态,就可用图解法在Y—X图上,或用其他方法求出理论塔板数Nt。精馏塔的全塔效率Et为理论塔板数Nt与实际塔板数N之比,即:
Et=Nt/N
影响塔板效率的因素很多,大致可归结为:流体的物理性质(如粘度、密度、相对挥发度和表面张力等)、塔板结构以及塔的操作条件等。由于影响塔板效率的因素相当复杂,目前塔板效率仍以实验测定给出。
精馏塔的单板效率Em可以根据气相(或液相)通过测定塔板的浓度变化进行计算。
若以液相浓度变化计算,则为:
Eml=(Xn-1-Xn) / (Xn-1-Xn*)
若以气相浓度变化计算,则为:
Emv=(Yn-Yn+1)/ ( Yn*-Yn-1)
式中:X n-1 第n-1块板下降的液体组成,摩尔分率
Xn第n块板下降的液体组成,摩尔分率
X n*第n块板上与升蒸汽Yn相平衡的液相组成,摩尔分率
Yn+1第n+1块板上升蒸汽组成,摩尔分率
Yn第n块板上升蒸汽组成,摩尔分率
Yn*第n块板上与下降液体Xn相平衡的气相组成,摩尔分率
在实验过程中,只要测得相邻两块板的液相(或气相)组成,依据相平衡关系,按上述两式即可求得单板效率Em。
三、实验装置
图精馏塔实验装置
1、精馏塔。本装置精馏塔体和塔板均采用不锈钢制作,塔径为Ф50mm,塔板数13块,板间距100mm,孔径为2mm,开孔率为6%。为便于实验时观察操作工况,特设置了两节玻璃塔节。精馏塔设置了两处进料口,同时在再沸器上也设置了进料口,以便于开车时直接向再沸器加料。本精馏塔的回流比通过回流控制阀和馏出液控制阀可以任意调节。
2、冷凝器。精馏塔冷凝器壳体采用不锈钢制作,换热管采用传热效率较高的铜管制作。管径为Ф12×1mm,换热面积为0.0568m2,冷凝器下部与精馏塔体直接相连以减少热损失。冷凝液储存在馏出液槽中,一部分通过回流控制阀和转子流量计计量后再返回精馏塔顶板。另一部分则通过馏出液控制阀和转子流量计计量后送至产品槽。
3、再沸器。精馏塔再沸器直接置于精馏塔下部,采用不锈钢制作,内置电加热管加热。总加热功率为2000W,分两组,各1000W,采用自动无级控制,承担精馏塔的温度控制调节,以确保控温精度。
4、料液泵。料液泵采用微型小流量离心管道泵,流量为0.4m3/h,扬程为6m,输入功率为150W,允许汽蚀余量(NPSH)r为2.3m。进行连续精馏实验时可通过加料出口阀、流量计向精馏塔加料。
5、控制屏。装置的釜液加热温度的给定和调节、加料量的调节、回流比的调节、离心泵出口流量的调节以及塔釜、塔顶温度、料液温度的显示、加料量、产品量、回流量和离心泵出口流量的显示,均集中在控制屏。精馏塔的料液槽、产品槽、以及料液泵也集中设置在控制屏内部(下部)。控制屏的后门可以打开,以便加料及维修用。
6、玻璃塔节。为便于实验时观察塔内的操作工况,本装置特别设置了两节玻璃塔节。为防止泄漏,玻璃塔节和两端法兰采用密封连接。在使用过程中,应尽量不拆开玻璃塔节为宜。
四、操作步骤及注意事项
1、精馏塔的正常与稳定操作
精馏塔从开车到正常稳定操作是一个从不稳定到稳定、不正常到正常的渐进过程。在这一过程中,塔内的浓度分布会从不正常到正常,经历“逆行分馏”之后,才会转入正常操作状态。因为刚开车时,塔板上均没有液体,蒸汽可直接穿过干板到达冷凝器,被冷凝成液体后再返回塔内第一块塔板,并与上升的蒸汽接触。而后,逐板溢流至塔釜。因为首先返回塔釜的液体经过的板数最多,从而经过的气液平衡次数也最多,显然首先到达最底下一块塔板的液体其轻组分的含量必然是最高的。而第一块塔板上的液体中轻组分的含量反而会比它下面的塔板上的液体中轻组分的含量低一些,这就是“逆行分馏”现象。从“逆行分馏”到正常精馏,需要较长的转换时间。对实验室的精馏装置,这一转换时间至少需30分钟以上。而对于实际生产装置,转换时间有可能超过2小时。所以精馏塔从开车到稳定、正常操作的时间也必须保证在30分钟以上。判断精馏塔是否已经进入正常、稳定操作状态,必须经过采样分析才知道。如果在同一采样点连续三次采样分析(至少两次,间隔10分钟以上)结果均相近(不超过1%),则可认为已进入正常、稳定操作状态。
2、维持精馏塔正常稳定操作的条件
①根据给定的工艺要求严格维持物料平衡
若总物料不平衡,进料量大于出料量,会引起淹塔;反之,若出料量大于进料量则会导致塔釜干料。从精馏的组分衡算方程:FXfi=DXdi+WXwi,我们可以导出:D/F=(Xfi-Xwi)/(Xdi-Xwi);W/F=1-D/F。两式告诉我们,在F、Xfi、 Xdi、 Xwi一定的情况下,还应严格保证馏出液D和釜液W的采出率满足组分衡算的要求。如果采出率D/F过大,即使精馏塔有足够的分离能力,在塔顶仍不能取得合格的产品。
②根据设计要求,严格控制回流量
在塔板数一定的情况下,对于精馏操作必须有足够的回流比,才能保证有足够的分离能力来取得符合工艺要求的产品。要取得合格的产品,必须严格控制回流量(L=RD)以保证足够的回流比。
③严格控制精馏塔内的气液两相负荷量,避免发生不正常的操作现象
漏液、雾沫夹带与液泛是精馏塔常见的非正常操作现象。板式塔的正常操作工况有三种,即鼓泡工况、泡沫工况和喷射工况。大多数精馏塔均在前两种工况下操作。因此,正常操作时板上的液层高度应控制在板间距的1/4以内,最多不超过1/3,否则会影响塔板的分离效率,严重时会导致干板或淹塔,使塔无法正常操作。操作时,塔内的两相负荷量可以通过调节塔釜的加热负荷与塔顶的冷却水量来控制。
④严格控制塔压降
塔板压降可以反映塔内的流体力学状况,根据塔釜压力表压降的变化可以及时调整塔的加热负荷与冷却水量,以控制塔的稳定正常操作。在实际生产中,塔板压降还可以反映塔板上的结构变化(如结垢、堵塞、腐蚀等),尽早了解,以便及时处理。
⑤严格控制灵敏板温度
灵敏板是指温度随组成变化最大的塔板。精馏操作因为物料不平衡和分离能力不够所造成的产品不合格现象,可早期通过灵敏板温度的变化来预测,然后采取相应的措施以保证产品的合格率。塔釜加热量的大小,可直接反映在灵敏板温度上,所以严格控制灵敏板的温度是保证精馏过程稳定操作的有效措施。灵敏板的温度是通过塔釜的加热量来控制的,塔釜加热量可通过调压器改变塔釜电加热器输入电压的大小来调节。在实验操作时,在初始开车阶段,首先可将控制屏上的“加热”开关打开,待相应的绿色指示灯亮后,将“温度控制”调整器的电源开关拨至“ON”,再将“手动—自动”开关拨至“手动”,将功率控制在1.5KW左右,打开冷却水,应随时观察灵敏板的温度变化;待塔板上开始鼓泡后,即逐步降低功率,同时还必须通过玻璃塔节随时观察塔板上泡沫层的高度变化,严格控制在板间距的1/4—1/3 之内,正常操作时应控制在1—2KW之间。一般情况下,塔板上液层(泡沫层)的变化,会滞后于塔釜的温度变化2~3min,操作人员发现塔板上液层(泡沫层)上涨或下降,必须立即采取措施,以防止发生严重雾沫夹带、液泛、淹塔和漏液、干板等不正常的操作现象,确保精馏过程的正常稳定操作。待操作状态基本稳定之后,同时将“设定温度”设定为稳定操作状态下的灵敏板温度,再将“温度控制”调整器的“手动—自动”开关拨至“自动”,此时温度调节器可根据预先设定的温度自动调节塔釜的加热温度。当环境温度较高时应将手动“调节1、2”电位器关小,以防止电加热功率过大(热惯性过大),温度难以稳定,以确保精馏塔能在有效控制状态下稳定操作。
3、产品不合格时的调节方法
①由于物料不平衡而引起的不正常现象及调节
在操作过程中,要求维持总物料的平衡是比较容易的,但要求保证组分的物料平衡则比较困难,因此精馏过程常常会处于物料的不平衡条件下操作。在正常情况下,对于精馏过程应有:DXdi=FXfi-WXwi,如果在 DXdi>FXfi-WXwi情况下操作,显而易见,随着过程的进行塔内轻组分将大量流失,重组分逐步积累,致使操作日趋恶化。
表观现象是:塔釜温度合格,塔顶温度逐渐升高,塔顶产品不合格,严重时馏出液会减少。造成这一情况的直接原因是:a.进料组成有变化,轻组分含量下降;b.塔釜与塔顶产品的采出比例不当,即 D/F>(Xfi-Xwi)/(Xdi-Xwi)。处理方法是:如果是原因b,可维持加热负荷不变,减少塔顶采出,加大塔釜采出量和进料量,使过程在DXdi< FXfi-WXwi的情况下操作一段时间,待塔顶温度下降至规定值时,再调节操作参数使过程在 DXdi=FXfi-WXwi的状态下操作。如果是原因a ,若进料组成的变化不大,调节方法同b。如果进料组成的变化较大,则需改变回流量或调整进料位置。
如果在DXdi<FXfi-WXwi情况下操作,则恰与上述情况相反,其表观现象是:塔顶合格而塔釜温度下降,塔釜采出不合格。造成的直接原因是:a.进料组成有变化,轻组分含量上升;b.塔釜与塔顶产品的采出比例不当,即 D/F<(Xfi-Xwi)/(Xdi-Xwi)。处理方法是:如果是原因b,可维持回流比不变,加大塔顶采出,同时应增加加热负荷,必要时还可适当减少进料量,使过程在DXdi> FXfi-WXwi的情况下操作一段时间,待塔顶温度下降至规定值时,再调节操作参数使过程在DXdi=FXfi-WXwi的状态下操作。如果是原因a,亦可按上述方法调节,必要时可调整进料板的位置。
②生产调节的变化引起的不正常操作的调节
人为因素或偶然因素导致进料量的变化(可由进料的流量计看出)引起的不正常操作,可直接调节进料阀门的开度使之恢复正常。如果是生产需要有意改变进料量,则应以维持生产的连续稳定操作为目标进行调节,使过程仍然处于DXdi=FXfi-WXwi的状况下操作。
③进料温度的变化引起的不正常操作的调节
进料温度的变化对精馏过程的分离效果有直接影响的,因为它会直接影响到塔内的上升蒸汽量,易使塔处于不稳定操作状况。严重时还会发生跑料现象。如果不及时调节,后果是严重的。发生此类情况,主要是通过调整加热负荷来解决。
④进料组成的变化引起的不正常操作的调节
进料组成的变化引起的不正常操作的调节方法同①,但不如进料量的变化那样容易被发觉(要待分析进料组成时才可能知道)。当操作数据上有反映时,往往会滞后,因此如何能及时发觉并及时处理在精馏操作中是经常要遇到的问题,应引起高度重视。
4、塔板效率
对于板式塔来讲,塔板效率是综合概括塔板上的气液接触状况和各种非理想流动对过程影响的重要参数。塔板效率又分为点效率、莫夫里板效率和总板效率。总板效率是板式塔分离性能的综合度量,它不仅与影响点效率、板效率的各种因素有关,而且还把板效率随组成而变化的特性也包括在内。精馏塔的总板效率在没有可靠的经验数据可用时,尤其是对于新物系,一般都由实验来测定。
总板效率的测定可以其定义式为依据,即:
η=Nt/N
定义式中的理论塔板数Nt可由X-Y图图解得到(必须注意:由X-Y图图解获得的梯级总数已包含精馏塔的塔釜在内,减去1之后才是精馏塔的理论塔板数),实际塔板数N则可以直接从已有的实验装置取得(本实验装置为13块)。而图解Nt,必须有正常、稳定操作状况下的馏出液与釜液的组成数据,以及相应的进料组成与热状态参数数据。这只能通过精馏实验才有可能取得。
由X—Y图的图解原理可知,精馏过程如果在全回流条件下操作,操作线就是对角线,此时只需要知道馏出液与釜液的组成Xd、Xw便可以进行图解。这样做可使实验过程更为简单。根据以上分析,我们就可以基本确定总板效率测定的实验步骤为:a.按操作规程开车,在全回流条件下进入正常、稳定操作状态后,调整有关控制参数使精馏过程符合工艺要求,然后同时取样分析馏出液与釜液的组成;b.数出精馏塔的实际塔板数N;c.由气液平衡数据绘制X-Y图,由Xd、Xw图解理论塔板数Nt;d.由定义式η=Nt/N求取η值。
如果要测定不同组成时的总板效率,则还需改变料液的组成,多测几组数据。
5、操作步骤
A、精馏塔总板效率测定(全回流)
(1)打开冷却水阀和塔顶放空阀26,从塔顶取样口24放空塔顶冷凝器中残夜,并检查馏出液槽的进口阀27是否已经关闭(必须关闭);
(2)检查塔釜的液位是否在液位计的最上位置;
(3)打开电源及电加热器开关,并将电流调至最大(顺时针方向);
(4)待从玻璃塔节处看到塔板已完全鼓泡后,将电流调回至4~6A,以控制塔板上的泡沫层不超过塔节高度的40%,防止过多的雾沫夹带;
(5)稳定操作20~30min后,可开始从塔顶、塔釜取样口24、25同时取样分析;
(6)如果连续2次(时间间隔应在10min以上)的分析结果的误差不超过5%,即认为已达到实验要求。否则,需再次取样分析,直至达到要求;
(7)完成实验后,先关闭加热电源,待塔板上完全干板后再关闭冷却水阀。
B、精馏塔连续操作实验(部分回流)
(1)打开冷却水阀和塔顶放空阀,从塔顶取样口放空塔顶冷凝器中残夜;
(2)检查塔釜的液位是否在液位计的最上位置;
(3)打开电源及电加热器开关,并将电流调至最大(顺时针方向);
(4)待从玻璃塔节处看到塔板已完全鼓泡后,将电流调回至4~6A,以控制塔板上的泡沫层不超过塔节高度的40%,防止过多的雾沫夹带;
(5)稳定操作20~30min后,可开始从塔顶、塔釜取样口同时取样分析;
(6)如果连续2次(时间间隔应在10min以上)的分析结果的误差不超过5%,即认为已达到开车要求。否则,需再次取样分析,直至达到要求;
(7)打开塔顶馏出液槽的进口阀和放空阀,开始控制开度小一些,以保证塔板上的操作稳定,操作20~30min后打开回流流量计阀门开始部分回流操作,并打开产品流量计阀门15开始出料(控制回流比小一些,以确保产品含量达到90%以上)至产品瓶8,同时还要启动进料泵5(先灌水、检查出口阀是否全关闭),再打开泵出口阀16和上进料阀12,控制流量稍大于产品流量,以确保物料平衡;
(8)精心稳定操作,每隔20~30min分析一次产品,以确保产品质量,并随时检查塔釜液位,若超过最高显示刻度,则应放出部分釜液(不得低于最低控制线);
(9)待获得的合格产品量达到500ml以上,达到实验要求;
(10)完成实验后,先关闭加热电源,待塔板上完全干板后再关闭冷却水阀。
6、注意事项
(1)开车前应预先按工艺要求检查(或配制)料液的组成与数量;
(2)开车前,必须认真检查塔釜的液位,看是否有足够的料液(最低控制液位应在液位计的中间位置);
(3)预热开始后,要及时开启冷却水阀和塔顶放空阀,利用上升蒸汽将不凝气排出塔外;当釜液加热至沸腾后,需严格控制加热量;
(4)开车时必须在全回流下操作,稳定后再转入部分回流,以减少开车时间;
(5)进入部分回流操作时,要预先选择好回流比和加料口位置。注意必须在全回流操作状况完全稳定以后,才能转入部分回流操作;
(6)操作中应保证物料的基本平衡,塔釜内的液面应维持基本不变;
(7)操作时必须严格注意塔釜压强和灵敏板温度的变化,在保证塔板上正常鼓泡层的前提下,严格控制塔板上的泡沫层高度不超过板间距的1/3,并及时进行调节控制,以确保精馏过程的稳定正常操作;
(8)取样必须在稳定操作时才能进行,塔顶、塔釜最好能同时取样,取样量应以满足分析的需要为度,取样过多会影响塔内的稳定操作。分析用过的样液应倒回料液槽内;
(9)停车时,应先停进、出料,再停加热系统,过4~6分钟后再停冷却水,使塔内余气尽可被完全冷凝下来;
(10)严格控制塔釜电加热器的输入功率,必须确保塔釜内的料液液面不低于最低控制线(塔釜加热管以上),以免烧坏电加热器,在投入自动控制后,还必须注意关闭加热开关,除非环境温度太低,使用一组电加热丝无法达到需要的控制温度,方可同时使用;
(11)开启转子流量计的控制阀时不要开得过猛,以免冲坏或顶死转子。
五、数据计算与处理
根据实验所得数据计算精馏塔在一定条件下的总板效率。
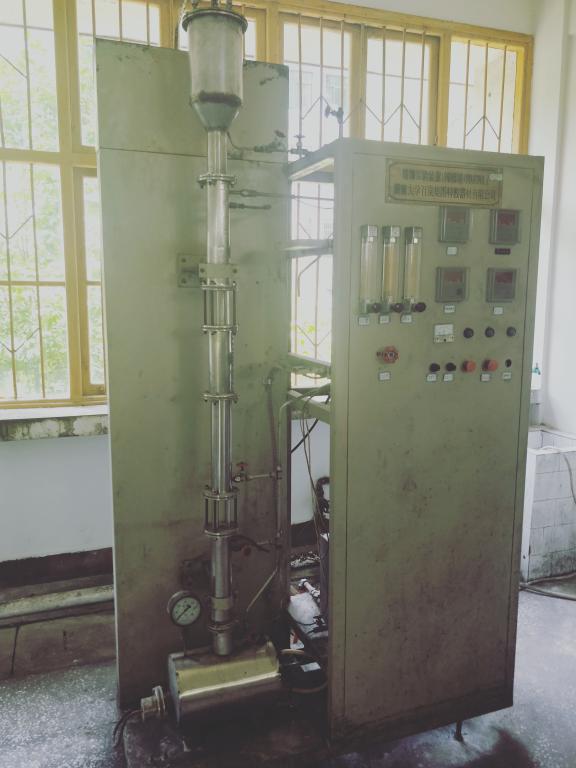 |
设备全图 |
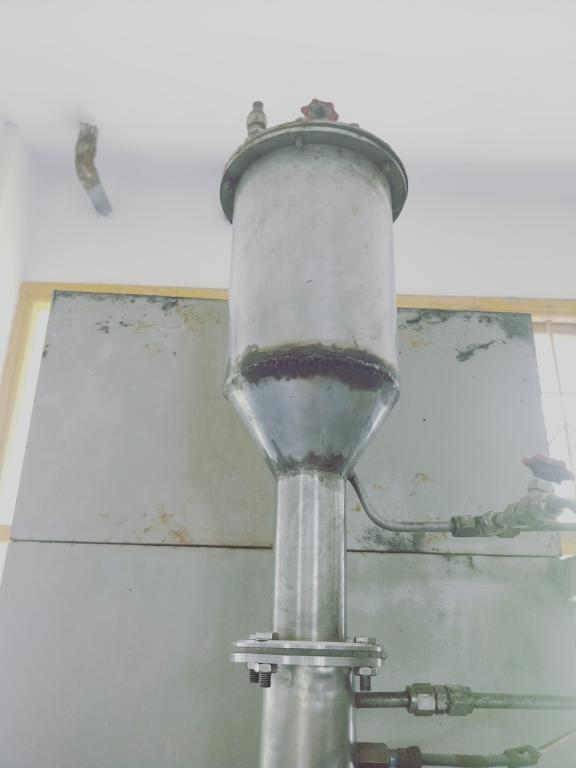 |
塔顶 |
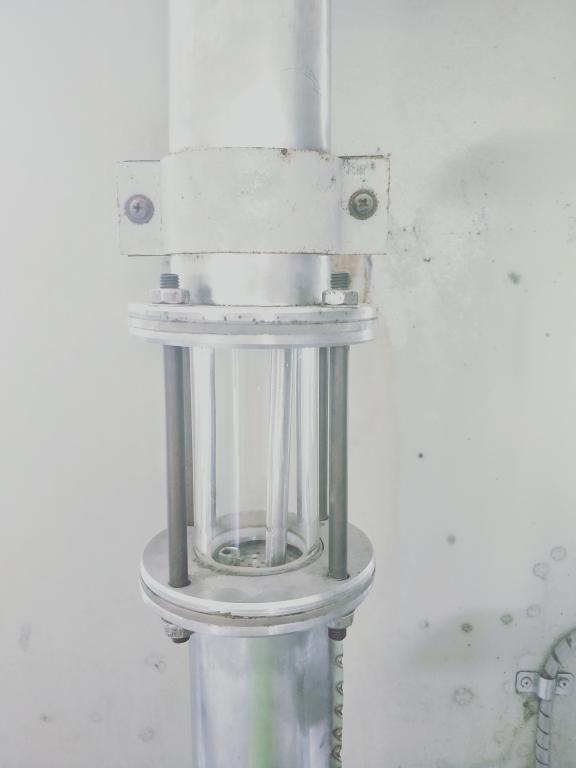 |
塔节 |
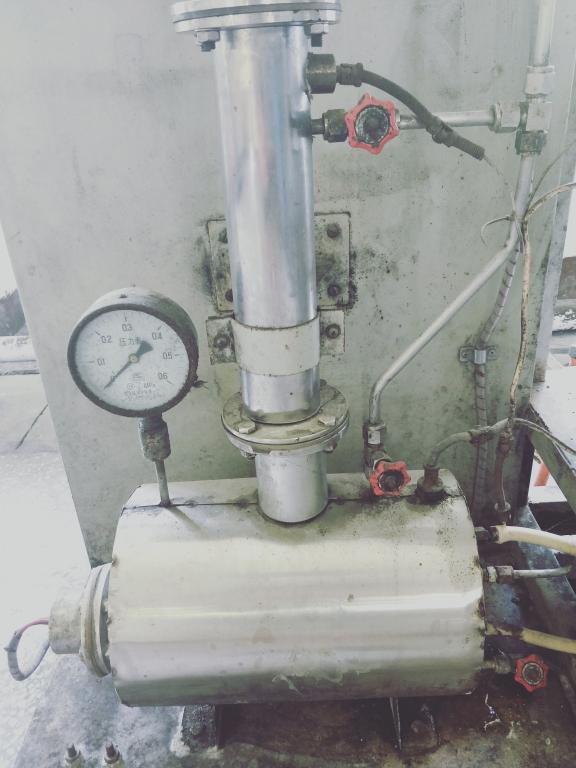 |
塔釜 |
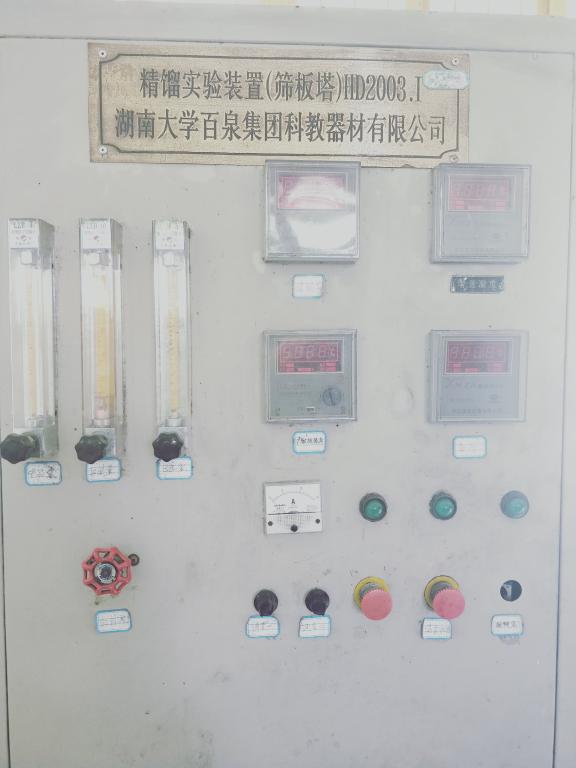 |
操作面板 |
 |
冷却水 |
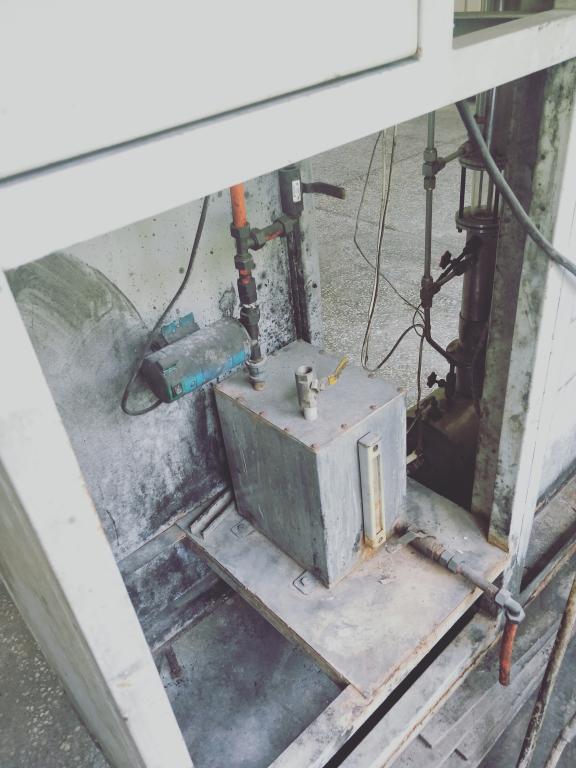 |
加料 |